Look around any modern neighborhood, and you'll spot the answer: most homes are built with concrete. This isn’t just a random trend. Concrete is the champion in home construction, found in everything from foundations to driveways and sometimes even the walls themselves. You’ll see it because it’s strong, doesn’t burn, and lasts forever if you keep water out of it.
If you’ve ever watched a house being built, that gray stuff trucks pour into molds is concrete—the backbone for everything above it. Builders love it because it can take massive weight and it sort of shrugs off storms, floods, and bugs. Even if the rest of your house is wood or steel, odds are your home sits on a concrete base.
Now, cost matters, too. Concrete isn’t the cheapest material out there, but compared to the headaches of repairing a rotten wood frame or rusty steel beams, homeowners often think it’s worth the price. Another cool thing? Engineers and architects use concrete’s flexibility to shape wild designs—curves, slopes, and weird angles aren't a big deal once you get a solid mold and a crew who knows what they’re doing.
- Why Concrete Takes the Top Spot
- How Wood Competes with Concrete
- A Look at Steel and Other Challengers
- Tips for Picking the Right Material for Your Home
Why Concrete Takes the Top Spot
It’s not even a close race—concrete leads the way in modern home building. The reason is pretty straightforward: it's tough, stays put, and doesn’t let pests or fire ruin your day. That’s huge if you want your house standing for decades. Almost every new house uses concrete in its foundation, and in some regions, the entire house is built with it.
If you wonder why, check out these real-world numbers below. They show just how much concrete dominates compared to other options.
Material | Global Share in Residential Builds (%) | Key Strength |
---|---|---|
Concrete | Over 70 | Compression strength; doesn’t burn |
Wood | ~25 | Lightweight; easy to work with |
Steel | <5 | Bends under pressure; very strong |
Here’s why concrete gets picked so often:
- Strength and durability: Concrete doesn’t just stand up to wind, rain, and quakes. It shrugs them off. Engineers often design foundations to last at least 50-100 years, and that’s only possible with the right mix of sand, gravel, cement, and water.
- Fireproof: Unlike wood, concrete won’t catch fire. In fact, it blocks fire from traveling between rooms. That’s why most building codes prefer it for basements and garage walls.
- Pest resistance: Termites and other bugs don’t eat concrete (unless they have superhero powers). It’s sort of the fortress material for your house.
- Affordable maintenance: Concrete doesn’t rust or rot, so you don’t need to repaint it or worry about fixing holes. Usual repairs (like sealing cracks) are pretty cheap compared to replacing rotten wood beams under an old house.
Here’s a tip: pay attention to the concrete quality and who’s pouring it. Bad mixing or poor foundation prep leads to cracks—ask around for concrete crews with a good reputation. It’ll save you from headaches down the road.
How Wood Competes with Concrete
Even though concrete rules the block, wood has been a top pick in home construction for centuries, especially in places like North America. Why? It’s lighter, easier to handle, and most framing crews could probably build a wooden wall blindfolded (not recommended). Wood is also easier to change or fix if you ever want to redo a wall or put in a new window.
The biggest advantage? Speed. Building with wood usually goes way faster than with concrete. Plus, there’s less drying time. For families wanting to move in before the holidays or avoid a long rent overlap, wood’s the way to go. It’s also pretty affordable, especially if you stick with standard lumber and don’t get fancy with exotic hardwoods.
Here’s another surprise: wood is a natural insulator. This means it helps keep cold air out in winter and hot air out in summer—so you could save on heating and cooling. Just remember, wood does have some downsides. Termites love it. It can rot if it stays damp. And during wildfires, wood’s not going to win any awards for fire resistance.
Check out this quick side-by-side of the basics:
Feature | Concrete | Wood |
---|---|---|
Strength | Very High | Moderate |
Build Speed | Slow (needs time to cure) | Fast |
Cost (2024 avg. US) | $130 per yd³ (ready-mix) | $600 per 1,000 board feet (framing lumber) |
Pest Resistance | Excellent | Poor (needs treatment) |
Fire Resistance | High | Low |
Thermal Insulation | Poor | Good |
Want to make wood last? Builders today use pressure-treated lumber and chemicals to fight off bugs and rot. And in places prone to earthquakes, wood frames hold a big advantage because they flex when the ground moves, instead of cracking or breaking.
So, while concrete stays in the lead overall, wood is still a heavyweight when it comes to speed, insulation, and remodels. Picking between these two often comes down to your location, climate, and how much you worry about bugs eating your house before your kids grow up.
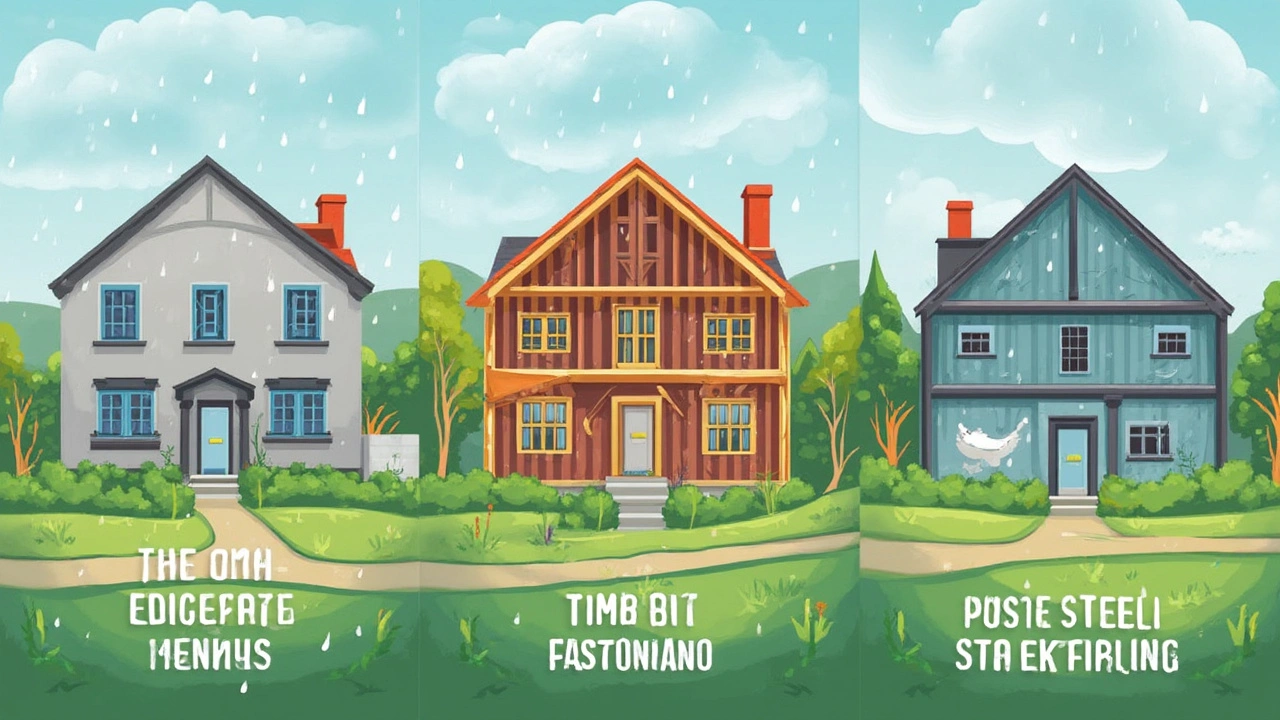
A Look at Steel and Other Challengers
Steel gets a lot of attention in the construction world. Walk into any city, and you’ll see skyscrapers and big commercial buildings relying on steel frames. But in home construction, steel isn’t quite as common as home construction pros might have you think. The big draw with steel is its strength—pound for pound, it beats out wood and concrete, making it a favorite for architects who want open floor plans or huge windows without extra walls in the way.
Here’s the catch: steel costs more. A steel frame house can run about 14% to 20% higher in initial material costs than a traditional wood-framed house. Add in the need for special tools and skilled workers, and costs go up again. You also have to watch for rust, especially in wet climates, unless you pay extra for coatings.
Still, steel isn’t all hard-to-handle headaches. It doesn’t burn, termites hate it, and it’s seriously tough against earthquakes and winds. For people in hurricane or earthquake zones, that’s huge. There are a few other materials showing up in new homes, too:
- Engineered wood: Stuff like cross-laminated timber (CLT) is big in eco-friendly homes. It’s strong and uses wood scraps, so you waste less.
- Brick and masonry: You’ll spot these more in older neighborhoods or areas with specific building codes. They’re heavy, slow to build with, and pricey, but they look cool and insulate well.
- Structural insulated panels (SIPs): These panels sandwich foam between two boards—fast to put together and great for energy savings.
Here’s a quick look at how these options stack up for someone thinking about building a home:
Material | Cost (per sq ft, avg) | Lifespan | Main Perks | Main Drawbacks |
---|---|---|---|---|
Steel | $20–$40 | 75+ years | Strong, fireproof, pest-proof | Cost, rust risk |
Engineered Wood | $15–$35 | 50+ years | Eco-friendly, fast to build | Moisture risk |
Brick/Masonry | $25–$45 | 100+ years | Durable, good insulation | Heavy, expensive |
SIPs | $13–$35 | 50+ years | Energy efficient, quick | Limited designs |
For most folks, these materials are interesting but not always practical. Still, steel makes a lot of sense if you want a house that’s going to stand up to pretty much anything nature throws at it. The others? Worth a look if you want a unique home or better energy savings, but plan to spend more time—or money—getting it right.
Tips for Picking the Right Material for Your Home
Picking what your house is made of isn’t just about style. There’s money, weather, maintenance, and even local code rules—yep, some areas flat out tell you what you can’t use. Here’s how to zero in on your best option without stumbling into mistakes that cost more down the line.
- Think about climate first. Live in tornado or wildfire country? Concrete wins for storm strength and fire resistance. In humid or termite-heavy areas, steer clear of untreated wood unless you're ready to fight bugs and mold every year.
- Compare upfront costs and the long game. Concrete and steel usually hit your wallet harder at the start. But if you play the long game—less rot, fewer repairs, better insurance rates—they often pay off. Wood is cheaper upfront, just watch out for future repairs.
- Check for earthquake risks. In places like California, flexible wood frames sometimes hold up better and are easier to retrofit than solid concrete.
- Ask about local building codes. Don’t get caught halfway through your dream home build because a rule bans your material choice. Most cities are strict, and some HOAs add more hoops.
- Think about energy bills. Insulated concrete blocks cut heating and cooling costs. Some modern wood options (like cross-laminated timber) work wonders for keeping homes cozy, too. If you’re all-in on green building, find out what works for your style and wallet.
Here’s a quick, real-world comparison to help sort things out. Prices change by region and time, but this table gives you a ballpark per-square-foot cost for materials:
Material | Average Cost per sq. ft. | Main Strength | Main Weakness |
---|---|---|---|
Concrete | $4–$8 | Flood/fire/storm resistant | Needs skilled work, tricky fixes |
Wood Framing | $3–$6 | Flexible, fast build, DIY-friendly | Termites, rot, burns easily |
Steel Framing | $7–$12 | Strong, bug-proof, doesn’t burn | Rust, price swings, needs insulation |
Bounce your choices off a builder or architect who knows your town. They’ve seen what actually works—not just what looks good in a brochure. Finally, don’t forget resale: people buying your house in the future care about this stuff too, even if you don’t plan on moving for years.